Unleashing Potential: The Hot Forming Spring Process
- lisa9031
- Feb 25
- 1 min read
Spring manufacturing encompasses a diverse range of techniques, each with its own unique advantages. Hot forming, a specialised process, stands out for its ability to produce springs with exceptional strength, durability, and complex geometries.
Unlike cold forming, which shapes the spring material at room temperature, hot forming involves heating the metal to a specific temperature, typically between 850°C and 1100°C. This elevated temperature significantly increases the metal's ductility, making it more pliable and easier to shape. The material becomes more malleable, allowing for the creation of larger diameter springs, intricate shapes, and complex geometries that would be difficult or impossible to achieve through cold forming.
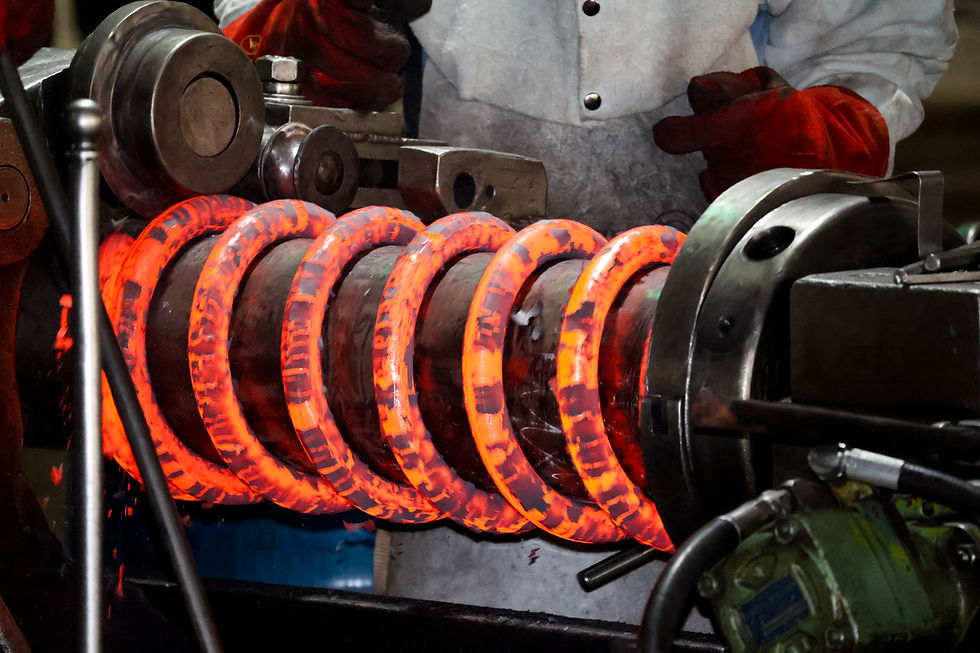
This enhanced formability translates to several key advantages:
Improved Strength and Durability: By reducing the risk of material cracking or deformation during the forming process, hot forming results in springs with superior strength and durability.
Enhanced Fatigue Resistance: The process can improve the resistance of the spring to repeated cycles of loading and unloading, crucial for applications that demand long-term reliability.
Versatility: Hot forming is suitable for a wide range of spring materials, including high-strength steels and alloys, each offering unique properties that can be tailored to specific application requirements.
At Woodhead Heavy Coiling, we possess the expertise and advanced manufacturing capabilities to effectively utilise hot forming techniques. We can leverage this process to produce high-quality, custom-engineered springs that meet the most demanding specifications.
Contact Woodhead Heavy Coiling today to discuss your specific spring requirements and explore how our hot forming expertise can help you achieve your project goals.
Comments